BNSF’s Continuous Improvement teams challenge the status quo to enhance service
BNSF is always working to raise the quality of our service for our customers as well as how we manage our operations. One way we do this is through the work of Continuous Improvement teams (CITs). Continuous Improvement is the process of identifying and analyzing problems and strengths, then testing and revising solutions.
“We have cross-departmental continuous improvement teams that are challenging the status quo, questioning all legacy assumptions and practices and leveraging new technology and data to drive their decisions with a focus on continuous improvement,” Jon Gabriel, vice president, Service Design & Performance, said.
Thanks to these teams, we’re becoming more efficient, creating additional capacity and improving the customer experience – and all by making the most of what we already have in terms of processes, existing equipment and other resources.
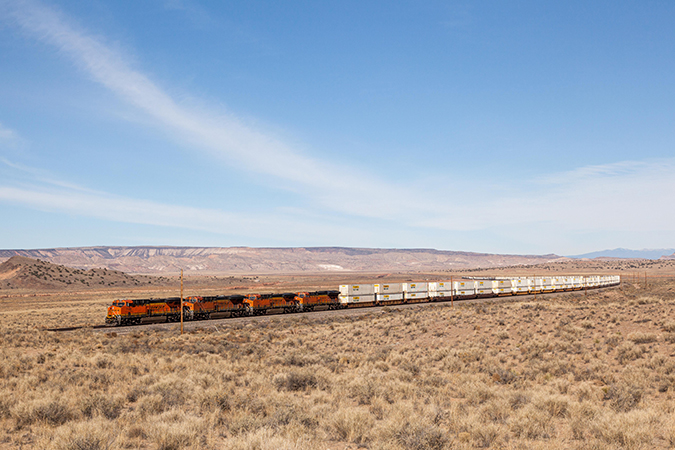
The process
The first step for each CIT is to define an issue that affects our ability to provide the best service. The teams collect historical data and analyze it to generate a baseline.
“Generally, an issue is when we’re not happy with our numbers,” Matt Garland, vice president, Transportation, said. That could be the time it takes to load containers onto a train or a lag in on-time performance. “With the data available today, we can put facts around what’s driving an issue vs. making assumptions. Plus, the speed of technology to analyze data is huge. What used to take weeks now can take an hour.”
After collecting and evaluating data, the team collaborates with end users, for example, team members who work in a hub or rail yard, to create potential initiatives and develop solutions.
“The bonds and relationships fostered by the CIT approach with everyone’s involvement help us to evolve while also challenging us to ask ourselves, ‘What if, what's next and why not?’” added Bob McConaughey, assistant vice president, Intermodal Field Transportation, and lead of the Intermodal CIT.
The next step in the process is for the team, working with employees in the field, to refine and implement solutions into daily operations.
The key is to make the solutions sustainable as well as scalable, Garland said. “Each location may vary, but we should be able to standardize processes. We should be able to take a person from one yard or terminal to another and they be able to apply the same process.”
In many respects what the CITs are doing is foundation building, Gabriel added. “With a company as large as ours, we are always in transition. If we can make small changes and cascade them across the network, there are big opportunities to make lasting changes.”
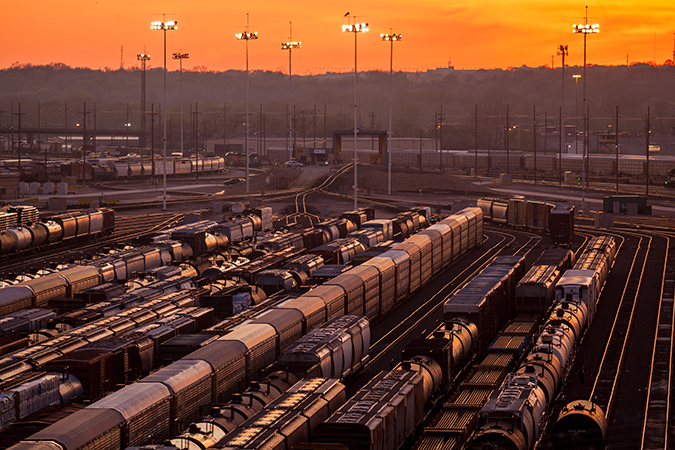
Merchandise CIT
In late 2019, our merchandise business was the first evaluated by this CIT.
The merchandise, or carload, business is just about anything that moves on a train that isn’t a container, trailer or shuttle/dedicated train (like a grain or coal train that hauls only one kind of rail car). Because it requires additional crews and lots of assets, like locomotives for industry switching or yard operations, if we can free those up, we can better serve our other customers’ business.
The team’s first charge was improving productivity at our hump yards, where freight cars are sorted by going over a “hump,” or hill, then using gravity to move them into a position. A terminal process control (TPC) system controls which track the car is sorted onto as new trains are built in “the bowl.”
The issue: reduce the time it takes to put cars “over the hill,” starting with our hump yards on the eastern part of our network where more of this business originates. (The team is now evaluating the western hump yards to eventually visit all eight across BNSF.)
“Those of us on the team have worked in a hump yard, so we know how the bowl is used, how to build trains and the switching processes,” Tanner Wyatt, general director, Transportation and leader of the team, said. “We took a deep dive with the local teams to understand the inefficiencies.”
They determined that the TPC program, installed about seven years ago, had capabilities that were not being fully realized. By fine-tuning the program for every hump and every bowl track, based on the type of freight car and each bowl track’s capacity, they were able to make processing more efficient.
“Working together on the program, we were able to reduce the ‘stop shorts,’ the cars that stall over the hump and don’t couple together,” Wyatt noted.
That’s just one of the issues the team helped resolve. They also reduced the number of switching operations that had to be completed within the hump yards by building better “blocks,” a group of cars routed for a common destination.
Wyatt also credits regular communication for our carload service improvements. “We have calls twice a day between the hump yards,” he said. “If one is in trouble, the others can plan accordingly and help.”
Following the team’s work at our eastern hump yards, hump productivity was at record levels, and today, there is 30% improvement across all of them.
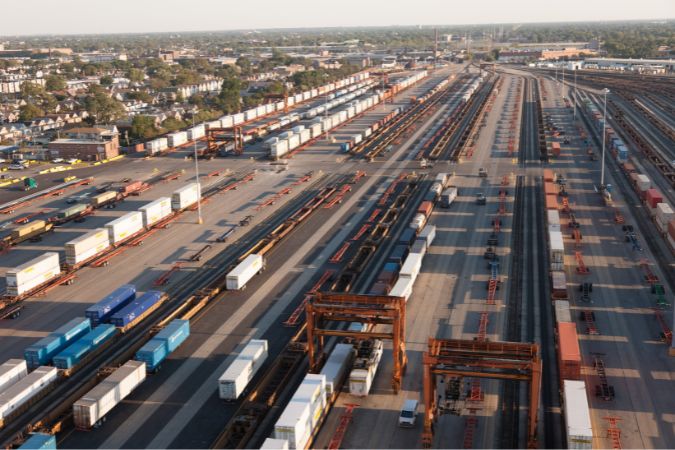
Intermodal CIT
Intermodal has high growth potential, so as this CIT finds ways to improve processes at our intermodal facilities, they’re also anticipating how the facilities will meet demands of the future. Their mission is to improve efficiency within hubs to create additional lift capacity and improve the overall experience for customers.
For more than a year, this CIT has been working with several intermodal hubs, including in Los Angeles and Chicago, some of BNSF’s busiest. The team has found opportunities for improvements that it can take systemwide.
One of these is at our Willow Springs Intermodal Facility southwest of Chicago. Here, as at other facilities, we want to ensure the right containers and trailers are efficiently located in parking lots to be placed trackside for outbound, departing trains.
Ronnie Johnson, general director, Hub Operations, supports this CIT. Using historical data and with input from the local team, the team’s solution was to create “hot lots” at Willow Springs.
“We know that there are units (containers and trailers) that need to be on an outbound train that tend to arrive close to cut-off (when a unit has to arrive at the facility to make a particular train departure date/time),” Johnson explained. “To accommodate these, we’ve created what we call ‘hot lots’ for those units to be parked in so we can have a shorter turn time from parking lot to a trackside railcar to load as we get closer to cut-off time.”
The hot lots are also set up to match the destination of the units to the correct train. Overall, this makes the parking lots more efficient. The team has also ensured directional operations through the facility, from ingate to unit parking to out-gate, that improves flow and reduces lot congestion.
“Willow Springs is a facility without readily available expansion property, as are many of our other intermodal facilities,” Johnson added. “This is another process that can be applied elsewhere to improve existing facility productivity.”
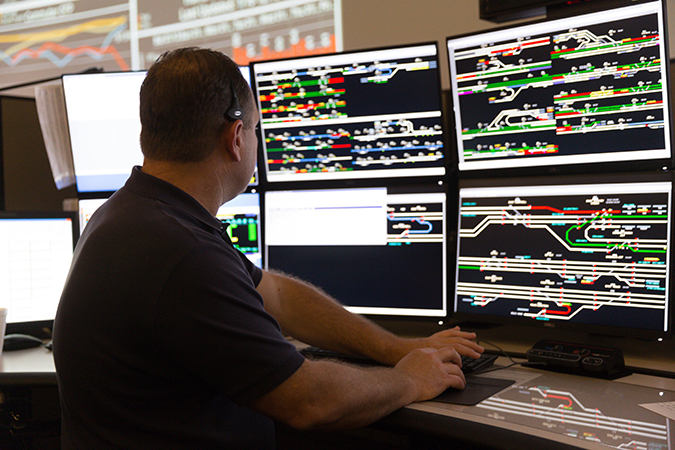
Network Operations Center CIT
At our Network Operations Center (NOC), our command center at our Fort Worth, Texas, headquarters, dispatchers work 24/7 over three shifts. Their job is to communicate with train crews to keep trains and other on-track equipment safely moving and on time.
Dispatchers use sophisticated technology to ensure the safe, fluid delivery of freight throughout our 32,500-route mile network. The most recent is Movement Planner, a planning application that allows data from multiple sources to be leveraged as trains move across the network. The plan is shared visually between different work groups, allowing for consistent execution.
“This is one of the most transformational technologies because it fundamentally changes for dispatchers the message received for their section of track. It puts one plan in harmony so our entire operations – 100-plus dispatcher desks over three shifts – have that view,” Ben Sharpe, assistant vice president, NOC, said.
With 10 divisions across our network, dispatchers are consecutively aligned division by division. As a train moves across our network, it crosses divisions, and that’s why dispatchers need that holistic view. The NOC CIT is working with dispatchers as the application is being rolled out, aiming to find ways to increase velocity and consistency.
For example, with their input and this new technology, we tested how to plan when Engineering teams conduct track maintenance on our Thayer (Missouri) North and Thayer South subdivisions on our Heartland Division. This single mainline track is about 300 miles long and sees all types of trains, including those headed to Memphis, Tennessee, our artery to the Southeast.
With high volumes on a single line of track, shutting it down for maintenance requires that all teams understand, agree and are ready for when these work windows are most opportune. “Movement Planner helped us to not only visualize where we could best place those windows, which are about six hours long, it also helped us to adhere to the schedule,” Drew Mayer, superintendent Corridor Operations, said.
Thanks to the technology’s real-time best-option view, train delay, which is unavoidable and necessary when track maintenance is scheduled, saw a 16% drop. Another benefit: the Engineering teams were able to plan their work and complete it according to the schedule instead of waiting for last-minute windows.
Like the other CITs, Sharpe recognizes that little incremental improvements can add up.
“There’s no silver bullet to continuous improvement,” he said. “It’s an evolving process that is going to improve our operations long-term to make everyone’s job easier and help us better serve our customers.”